今回ご紹介するVE事例は、いつもご紹介している設計上の工夫ではなく、筐体設計・製造.comを運営する岡部工業が保有するベンダーによるコストダウン事例になります。
通常、曲げ加工はベンダー(プレスブレーキ)を使って行いますが、このベンダーには下記の写真のように、1種類の金型しかセットができません。従って様々なサイズ・形状の曲げ加工が必要な筐体部品を加工しようとすると、都度金型を交換するか、もしくは必要な金型をセットした複数のベンダーを用意し、加工する必要があります。この場合、1ケあたりの筐体部品に必要な曲げ加工時間は、非常に長くなってしまうことは、お分かりいただけると思います。
その点、当社が保有するステップベンド機能を持つベンダーであれば、下の写真のように複数の金型を同時にセットできるので、作業者は左から右へセットされた金型の順に曲げていけば完成品に仕上げることができます。この場合、加工時間が非常に早くなります(従来のベンダーではスイッチであるフットペダルをベンダー中央部に置いて作業していたため、作業者は「足を伸ばしてスイッチを踏みつつ、曲げ作業をする」という難しい姿勢で加工する必要がありました。最新機種のベンダーではフットペダルが自動的に左右に移動するため、楽な姿勢で加工できるようになっています)。
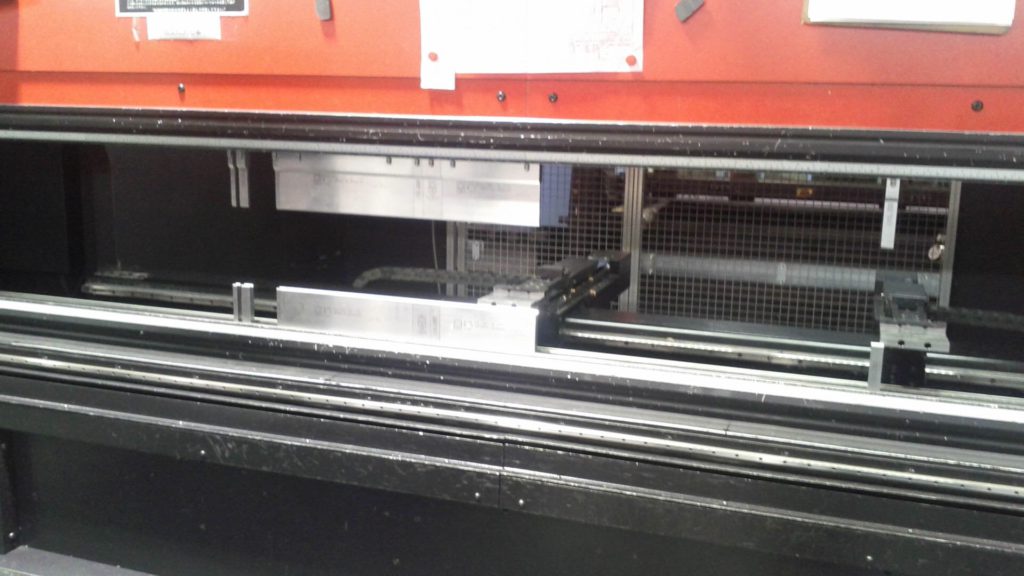
ステップベンド機能を持つプレスブレーキの金型の様子。 異なる金型が複数セットされていることが分かる。
筐体設計・製造.comが手掛けるような数百個にも及ぶような筐体部品の加工が必要な場合は、このステップベント機能があると、曲げの工程を集約でき、取り置き時間が削減できることで、飛躍的に生産性が高まります。
なお、ステップベンド機能がないプレスブレーキでも、金型の高さがすべて同じであれば理論的には一つの機械に複数の金型をセットすることで曲げ工程を完結できるかも知れませんが、そもそも金型にはグースネックなど通常の金型よりも長いものも存在しており、並べることができません。
このように、筐体設計・製造.comを運営する岡部工業では、お客様への日々のVE提案に加え、生産性の高い機器を積極的に活用することで、お客様のご要望に柔軟に応えて参ります。筐体の設計・製造、あるいは筐体の板金部品加工など、お困りのことがありましたら当社にお声掛け下さい。